When St. John residents David and Gina Gloski looked to rebuild their seaside home after it was damaged in a hurricane, durability and weather resistance were key considerations when it came to choosing the roof system. But aesthetics did not take a back seat. The restoration project included a stunning blue standing seam metal roof from Petersen, which made the house an instant landmark on the island.
In late 2017, the U.S. Virgin Islands were struck by Hurricane Irma, and the scope of the damage on St. John made rebuilding even more difficult. Luckily for the Gloskis, their home was a good candidate for restoration. “This was part of the project after we bought it — to put it back together again,” says David Gloski. “It was in decent shape. The structure was mostly there. The original roof was a corrugated tin roof that had to be completely replaced.”
The wood-framed house originally had a pool at its center, which was covered only by a screen. The roof restoration plan included covering the pool area. “It was never really enclosed before,” notes Gloski. “It was a true beach home. The hurricane basically blew right through the house.”
The project involved installing the standing seam metal roof system on the five roof areas that surrounded the pool area. A flat roof with two skylights was built to enclose the pool. It was topped with a silicone coating system from GE Silicones.
Finding the Right Roof
Vince Scapecchi of SeaView Building Solutions helped the Gloskis select the roofing components. The Gloskis were interested in a standing seam aluminum roof, and Scapecchi recommended Petersen’s Snap Clad Panel with two pencil ribs. The Gloskis chose the color — Interstate Blue — thinking it was perfect for the home, which they had christened “C’est La Sea.”
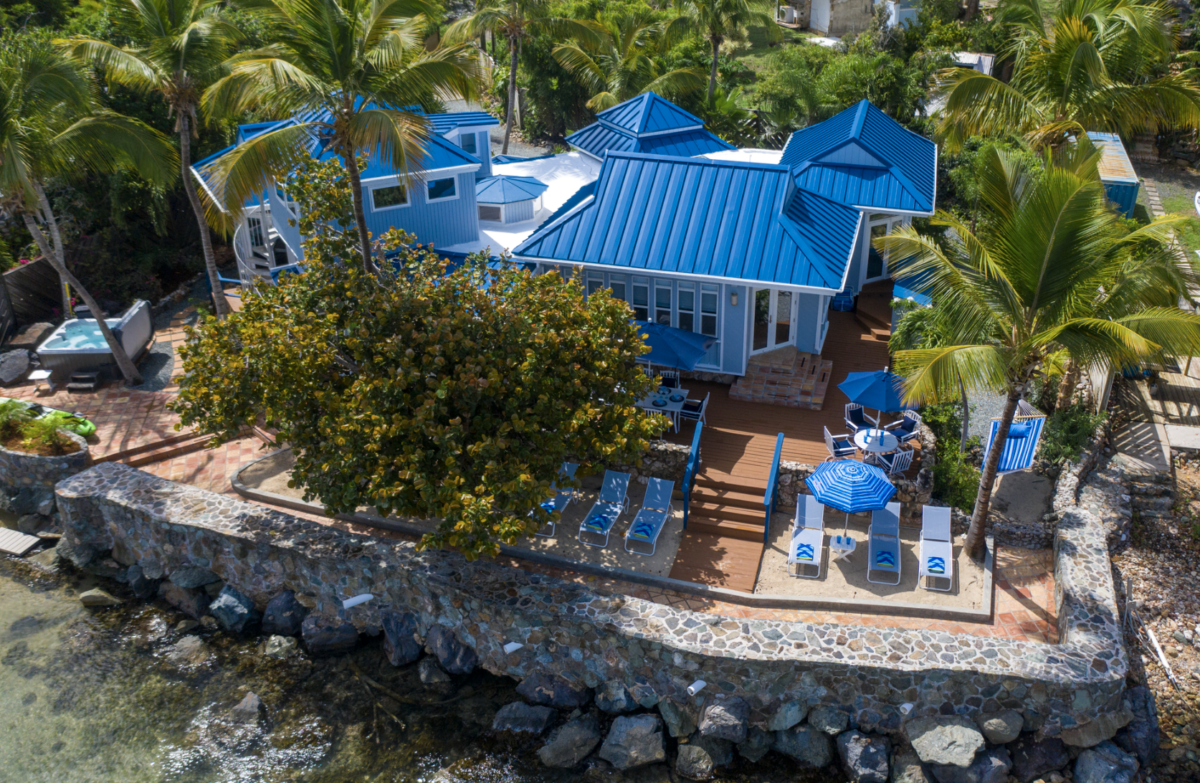
Durability was crucial factor in the decision-making process, as were the weight of the materials and their ability to stand up to the harsh oceanside environment. “Having a standing seam roof was important to us for leak resistance because we get lots of rain down here,” Gloski says. “It’s light, and we did not want a heavy burden on the home, which is older. We wanted aluminum, because it’s right next to the water and we didn’t want it to rust.”
Challenges included multiple roof areas and tricky details, including Pagoda-style roofs and a small cupola on the flat roof. One of the roof sections had to be lifted back into position because the building had settled.
The general contractor on the project was Dan Boyd of Lovango Enterprises. The vast majority of the roofing work was overseen by independent contractor Nathan Visel.
“Nathan had a really tough assignment,” notes Gloski. “Down there, labor is hard to come by, and right after the storm everybody was looking for repairs. Dan Boyd found a contractor who could do it and basically left him there. He worked on that project for a year. With all of those small roof areas, it became a bit of an art project for him.”
Challenging Installation
Visel came on board after the original roof had been removed. “I got out there just in time to weatherize the sheathing,” Visel recalls. “We put on the Grace Ice and Water Shield and started running with the panels themselves. We squared up and marked our lines. We did the biggest pitched roof first, and then moved on to the smaller ones.”
The metal panels were pre-cut to length. “We had virtually no field cutting,” notes Visel. “We just used a field brake on just the ends over the drip edge.”
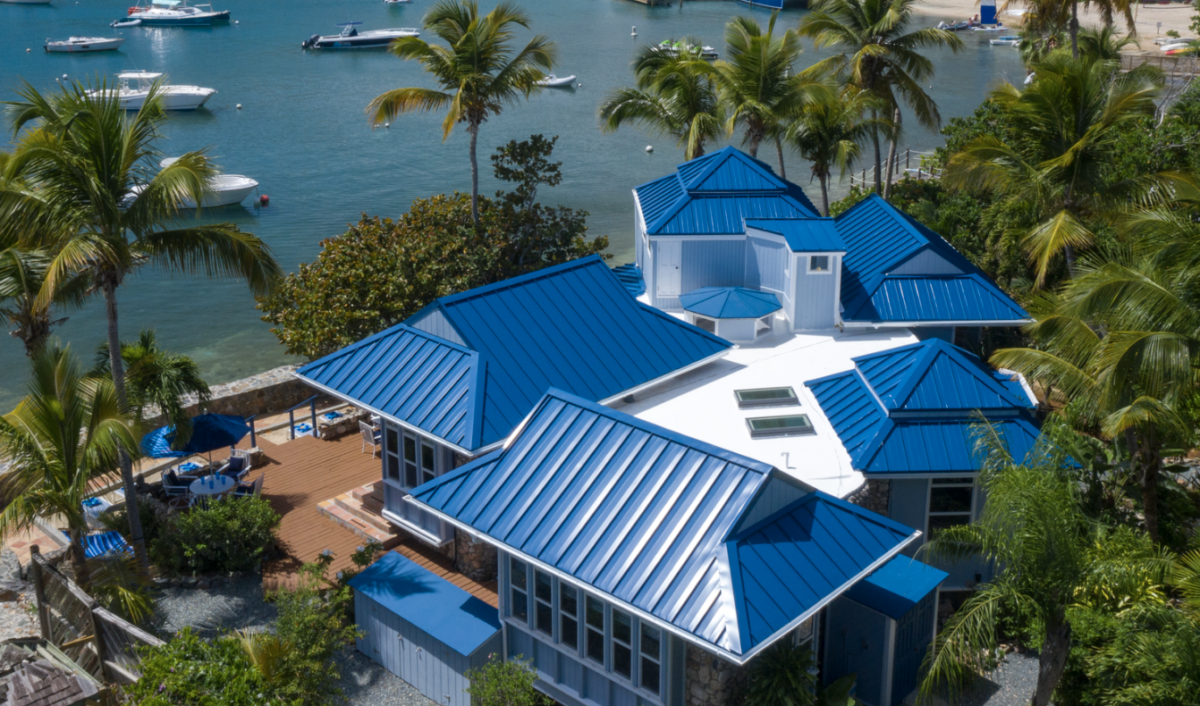
Crews also installed new gutters. “You don’t build houses down here without gutters because cistern water is our main form of house water,” Visel says. “The roof was designed with maximum surface area to collect as much water as possible. The entire flat roof is designed for water collection.”
The gutters were designed to divert water directly onto the flat roof, which in fact is slightly pitched to direct the water to internal drains leading to the cistern. Visel applied the white silicone coating, which had to have the durability to stand up to the flowing water as well as periodic maintenance, including clearing debris from the roof drains.
It was Visel’s first time installing the Snap Clad panels. “With any new product, there is always a learning curve, but it was a pretty straightforward operation,” he says. “It was a great product to work with once we figured out a viable strategy. And it’s held up to many storms since then. It’s a strong material; it’s a good system.”
Challenges on the project included coordinating deliveries and difficulty finding crew members. “Working down here, you will learn about five different trades,” Visel says. “Everything can be a challenge, including the logistics of finding materials. On the island, you don’t have the luxury of multiple options, and there can be shipping delays. ”
The weather was perhaps the toughest obstacle. “We have a wet season, and then in the dry season, it’s unpredictable, too,” Visel says. “You can have perfect blue skies, and then it can drop an inch of rain on you in an hour and a half. You just have to work through it.”
“You are working in very tight windows,” Visel continues. “It’s very hot and humid, but the sun is the real killer. We are so much closer to the equator here that you have to protect yourself. You don’t see many shirtless roofers here. We’re all in long sleeves and hoods.”
Winning the Battle
The project was a tough one, but Visel and the Gloskis are pleased with the result. “I enjoyed working on it,” Visel says. “That was by far the most elaborate roof I have ever done. It was wild. It was kind of a battle. We went through a lot of people and rotated some crews over the course of that job.”
Since his home has been restored, Gloski has seen more blue standing seam roofs pop up on the island. “I think we were one of the first to get that color,” Gloski says. “Everybody loves it. It’s a landmark for us. Everybody knows we are ‘the blue roof house’ — even if there are more of them down here now. It looks great, and it just changed the look of the whole house.”
If you’d like to check out the roof in person, C’est La Sea is also available for rent. For details, just visit cestlaseastjohn.com.
TEAM
General Contractor: Lovango Enterprises, St. John, U.S. Virgin Islands
Roofing Contractor: Nathan Visel, St. John, U.S. Virgin Islands
Distributor: Seaview Building Solutions, Pompano Beach, Florida, seaviewbuildingsolutions.com
MATERIALS
Metal Roof Panels: PAC-CLAD Snap Clad with Pencil Ribs in Interstate Blue, Petersen, pac-clad.com
Roof Coating: Enduris 3500, GE Silicones, siliconeforbuilding.com
Be the first to comment on "Blue Metal Roof Is the Crowning Touch for Restored Home in St. John"