As demand for renewable energy is increasing, photovoltaic (PV) arrays (also referred to as solar panels) are being considered for installation on roof areas more frequently. Proper planning can greatly reduce the potential for roof leaks, voided roof warranties, structural damage, and unnecessary expenses.
Prior to installing PVs, facility owners and managers need to determine if their roofs are good candidates for PV panels. For existing buildings, it is important to review the roof system and perform a structural analysis of the existing building prior to considering new rooftop PV panels. If you have a new building or are planning to build a new building, the 2015-2021 International Building Codes require roofs to be solar-ready. Even if solar is not installed when the building is constructed, the building will need to be designed to accommodate solar in the future. The new codes require that a structure’s roof system not only has to handle the live load, dead load, and snow loads, it also needs to have the built-in capacity to handle a solar/electrical distribution system as well.
You’ve Decided to Install Rooftop PV Panels: Now What?
Once you have decided to install PV panels on your roof, it is important to consider the age of your roof. A new building with a one- or two-year-old roof may require input from the roofing manufacturer who holds the warranty. A building with a roof that is between five and seven years old may need further evaluation to determine if the roof is in good enough condition to install a PV system on top of it. With older buildings, the roof needs to be evaluated to determine if the current roof will last for the lifespan of the PV panels. Needing roof repairs/replacement halfway through a PV system lifespan can be problematic and potentially costly in both construction costs and lost PV energy revenue.
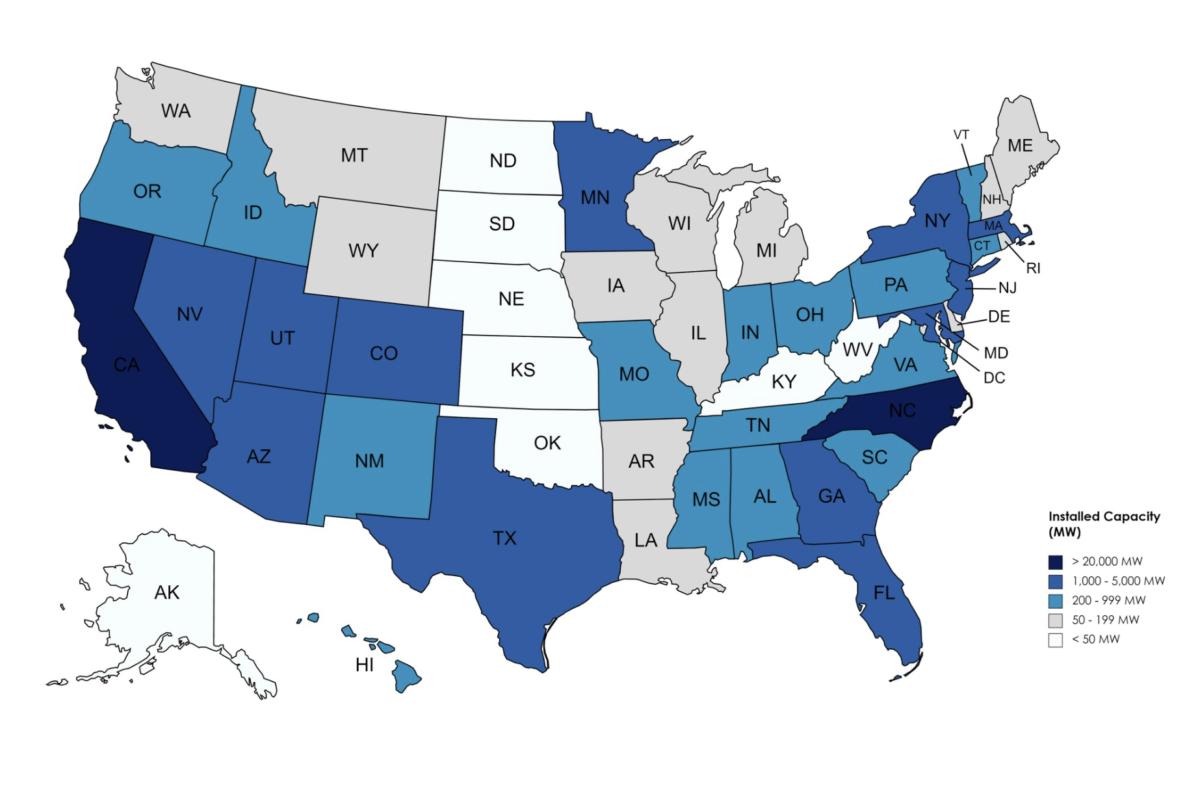
Evaluate the Existing Roof System: Repair or Replace?
For older roof systems, it is important to perform a full roof evaluation to determine the condition and then a cost-benefit analysis of repair vs. replacement. A current rule of thumb that some roof manufacturers use is that roof systems five years or older should be replaced prior to installing a PV system so that the lifespan of the roof better aligns with the PV system life span. This can vary depending on the roofing materials and manufacturers. The following methods are just a few of the options out there that can help establish a roof’s current condition:
• Infrared thermography (IR survey) detects the infrared energy emitted from an object to identify its temperature, which can indicate potential moisture and/or wet insulation within the roof system.
• Electric field vector mapping (EFVM) uses electric potential gradients, a voltmeter and electrical probes to detect roof membrane punctures and moisture intrusion. The IR may determine if there is wet insulation, but the EFVM will reveal where those pinholes are so the roof can be repaired before installing a PV system.
• Destructive test cuts can be used to identify system configurations and to confirm the findings in the infrared survey and EFVM.
Evaluate the Structure
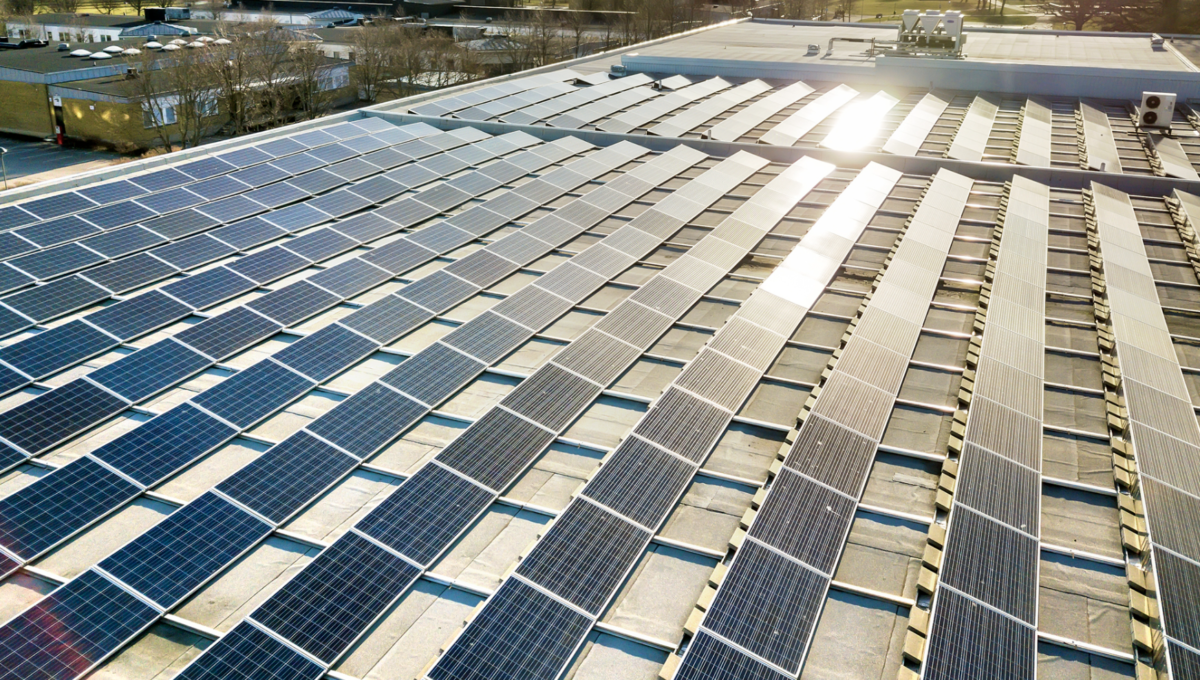
While new buildings are required to have planned capacity for PV systems built into the design; for existing buildings, it is important to determine if the roof deck and structural framing have the reserve capacity to handle the loads from a PV system. Although many panel manufacturers note that their systems weigh 5-6 pounds per square foot, the weight of the ballasts and actual point loading of the installed configurations can exceed these values and need to be considered. A full structural code review and structural analysis should be completed by a licensed structural engineer to review the wind loading, dead loading, seismic loading, and snow drifting design parameters for the PV system and how these affect the building’s structure. The available reserve structural capacity of the existing structure may dictate the type and mounting system for the proposed rooftop PV.
Designing a Roof For PV
Roofing materials that are noncombustible or self-extinguishing are preferred due to the increased fire risk under a PV system that comes with electric components. The fire ratings of both the roof system/roof cover and the PV system should be carefully considered when determining both the PV system and roof system to be installed. Membrane color is also an important consideration. Reflective roof membranes can help with the PV efficiency, as it helps to reflect light back up into the panels. White membranes are preferred under the PV system since black membranes heat up more in the sun, which reduces their efficiency and increases potential fire risk. Roof manufacturers may have specific requirements for minimum membrane thicknesses, walkway pad/slip sheet requirements, and other design items if a PV system is to be installed on the roof.
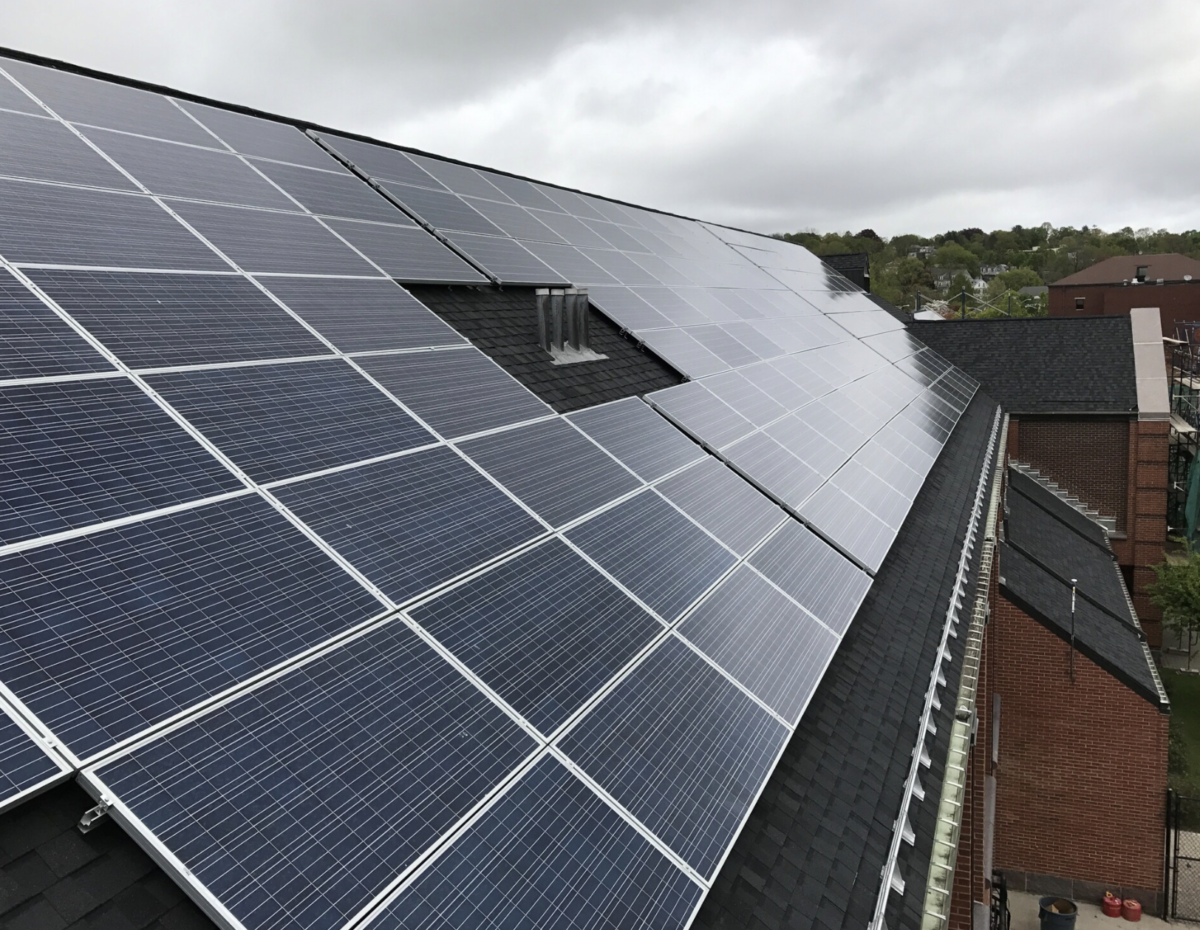
Adhered roof systems are more desirable for ballasted PV systems, as mechanically-attached single-ply membranes will have billowing effects that can displace the PV panel system and damage the roof below, as well as electrical conduits and connections. High-compression strength insulation (minimum 20–25 PSI) and non-combustible cover boards are preferable, as these provide better resistance for the additional weight that ballasted PV systems put on the roof. For any systems that are sitting on the roof, proper slip sheets and walkway protection pads are essential, especially under racks and along maintenance access routes. For fixed PV systems, attachment points need to provide enough height for proper roof flashings (8 inch minimum) and curb mounted systems need to be properly oriented to limit disruption to roof drainage.
Additional Design Parameters include:
• Fall protection and access: It can be tempting to extend PV layouts right to the roof’s edge to take full advantage of the roof area, but it is imperative to have safe access to not only the roof and PV systems but also to the mechanical units and firefighting operations. Ballasted rails work well for fall protection along roof edges. Structurally attached rail systems can be used if it is necessary to extend your PV system out further to the edge of the roof, but they may need additional structural upgrades and roof penetrations to handle the loading.
• Electrical equipment design coordination: PV systems require electrical components and conduits to be run across the roof and into the building. It is important to properly design these components and roof/wall penetrations to be watertight with consideration for future roof replacements and wall work. All roof penetrations should provide a minimum 8-inch flashing height above the roof (more is better if it can be done reasonably). All wall penetrations above roof systems should be placed a minimum 8 inches above the roof-to-wall flashing to accommodate future raising of these flashings. Additionally, electrical wiring and conduits should be properly routed around all rooftop PV panels and across roofs to avoid chafing/damage to wiring, which could increase the chances of electrical fires. Conduits will need to have proper expansion joints throughout the system to account for movement of the PV system, especially with ballasted PV systems.
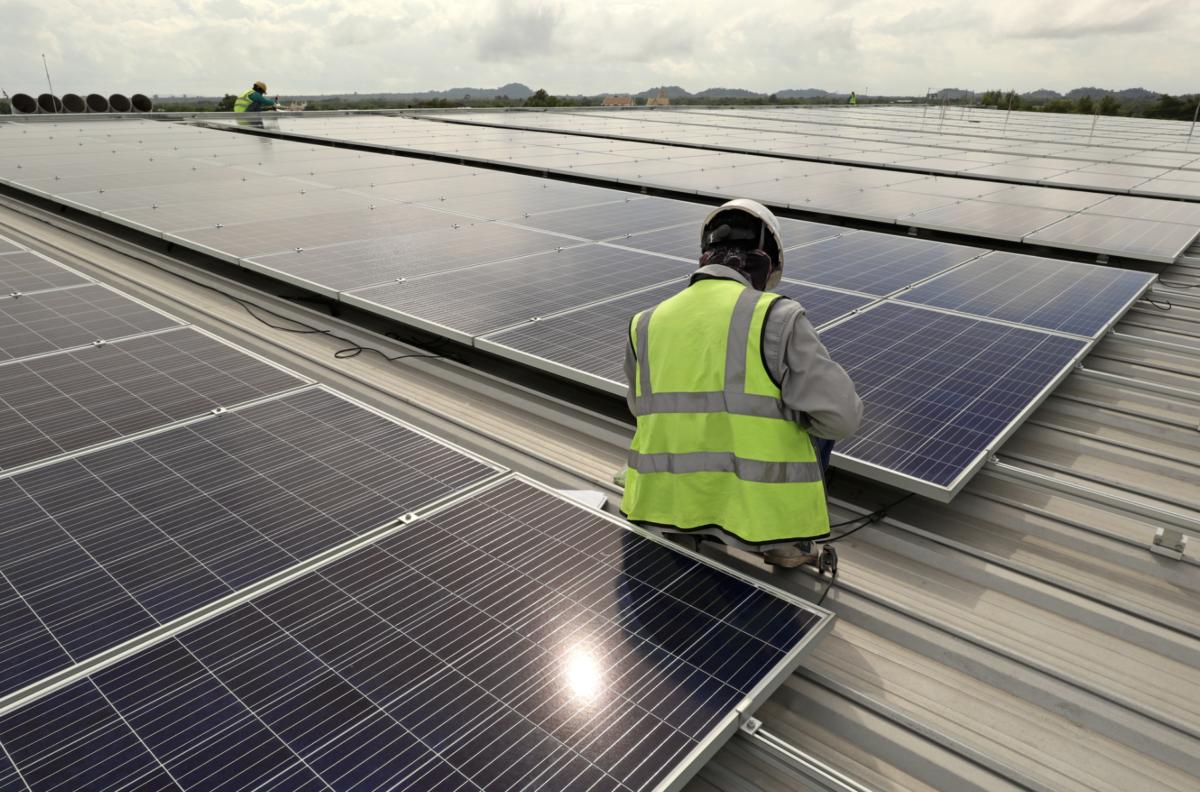
Selecting the Right PV System and Attachment for the Building
Once the PV panel type and ownership type are identified and the roof is found to be acceptable for PV installation, the layout and anchorage of the PV panels needs to be selected. Each PV system and attachment type has their own advantages and disadvantages to consider when determining the best system for your roof.
• Low-sloped roof curb systems: This system consists of panels attached directly to the structure through elevated curbs installed on the roof. Low-slope roof curb systems can be installed at steeper angles than ballasted systems. The greater angle allows the panels to capture and produce more energy, making them more efficient than ballasted systems. Due to the panels being lifted off the roof, it is possible for owners to perform roof repairs and maintenance below these systems. The addition of roof curbs can disrupt the drainage paths of the roof, so it is important to make sure curb layout aligns with the drainage slope of the roof system. The higher angle and attachment to the structure may also pose additional wind loads and snow drifts on the structure so it needs to be properly accounted for in the structural and attachment design. Additional framing may also be required to support curbs, which can increase overall costs for the installation.
• Low-sloped roof post systems: Low-slope roof post systems consist of dunnage above the roof with posts that go down into the roof and attach to the building’s structure. This system is similar to low-slope roof curb systems in that it can be installed at steeper angles than ballasted systems but doesn’t affect the drainage like curb systems due to the smaller post penetrations. The dunnage can also be raised high enough to accommodate future roof replacement and repairs not possible with lower roof mounted or ballasted systems. The additional roof penetrations can be problematic as more penetrations through a roof that require flashings can lead to a higher potential for leaks at these flashings. Low-slope roof post systems may also require additional structural design for the steel dunnage and support, and there is potential for additional wind loads and snow drifts because the panels have greater, raised angles. The post system option also directly connects the panel loading to the structural frame system and bypasses an underperforming roof deck.
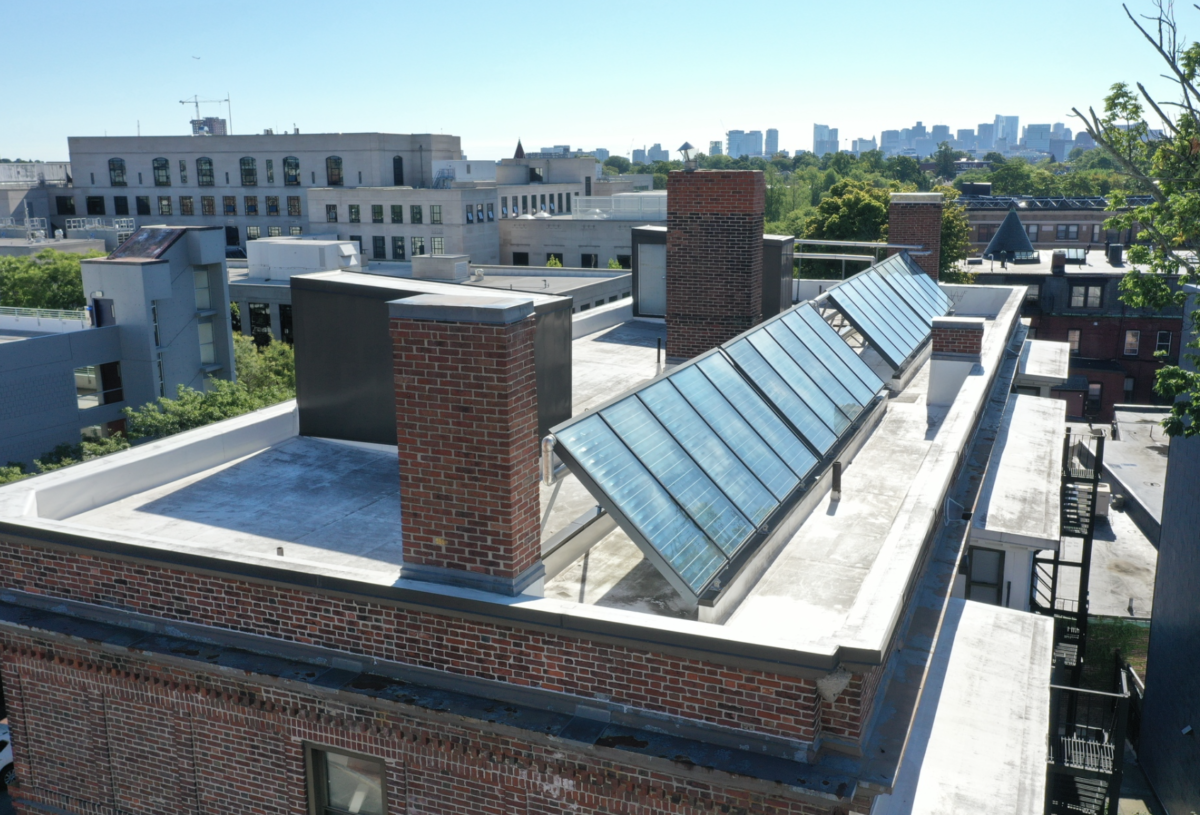
• Low-sloped roof ballasted systems: Ballasted rack systems are some of the most common systems used on low-sloped roofs, as they are relatively inexpensive because they rely on the existing roof system and deck for support. The panels are installed on a rack that is placed onto the roof surface and typically ballasted with concrete blocks. This system is easy to install, especially on an existing roof system, and has little-to-no roof penetrations for the framing and attachment of the panels. The ballast on this system does make this system heavier when compared to a curb or post system. The ballasted panels are not attached to the structure; therefore, they must be kept at a lower angle to avoid being displaced by wind, making the panels less efficient. Due to having direct contact with the roof system, it is important to coordinate their installation with the roof manufacturer and provide a slip sheet or walkway pad to protect the primary roof membrane.
• Low-sloped roof–roof manufacturer integrated systems: Manufacturers are developing more integrated systems where the roof system and panel system attachment are integrated into the roof system. The brackets are welded directly to the membrane in combination with attachment to the roof system. The single-source warranty with this option can be appealing to building owners.
• Steep-sloped roof systems: Steep-sloped roofing PV panels typically consist of rails that are either attached with clamps to the standing seam limiting roof penetrations or are attached through brackets that integrate directly into the shingle system. The panels are installed parallel to the roof surface, which may increase differential wind loading and the potential snow/ice buildup, requiring further analysis on a project-by-project basis. The PV panels may also complicate or obstruct access to the roof for maintenance and repair. Shingle roof systems, although easy to attach, require additional roof penetration, which can cause roof issues if incorrectly installed. Shingle roof systems are not recommended for retrofit applications because they could compromise the existing shingle roof during the installation. Since the PV panels have a smoother surface than shingles, there is increased potential for snow/ice sliding off the roof.
• Steep-sloped roof integrated systems: Emerging technologies include solar shingle and/or solar roofs where the roofing components themselves are the PV panels. These PV systems come in a variety of different shingle looks and offer aesthetic benefit as the PV systems are integrated into the cladding and appear similar to a normal roof as opposed to the traditional PV panel systems that are installed above or on the roofs. These systems are all relatively newer technology and have not yet been time tested.
Construction Coordination for Rooftop PV Systems
Proper coordination between the trades will help the project proceed as seamlessly as possible. The PV installer, roofer, electrician, facility personnel, roof manufacturer, designer, and Owner’s representative all need to understand the various steps, whether it is a PV removal on an existing roof replacement or a PV installation on a new building/roof. Not preparing the roof for PV panels can lead to unexpected costs years later should the PV panels need to be removed to accommodate roof repairs or replacement. A solar contractor will be required to remove and replace the units. Additional costs may be incurred to safely and properly store the removed panels. If you do not own the PV panels outright, there may be costs for damages or the loss of revenue that solar provider or investors will demand when their system is offline during the roof replacement. Solar contracts and agreements should be carefully reviewed as roofs and PV systems may have different life expectancies.
Financing Options – How Do I Pay for It?
There are a few options that building owners can consider when deciding how to finance a PV system. Solar leases/power purchase agreements (PPA) and solar loans/net metering are the two most prevalent options.
1. Solar leases/power purchase agreements (PPA) are arrangements where a third-party developer purchases, installs, maintains, and operates a PV system on your roof. The building owner benefits from free installation and a consistent price of electricity generated by their building, which is typically below market value. A PPA’s typical life span is about 20 years. PPAs can also include funding for roof replacements in the agreement.
2. Solar loans/net metering require building owners to purchase, install, and maintain the PV panels themselves. Building owners typically finance this purchase through a loan. The electricity that is generated by the PV panels is owned by the building owner and powers the building at no cost. If there is any excess power, it is sold back into the grid (net metering). Some states have different requirements for net metering, so those vary depending on the jurisdiction.
Don’t Forget the Maintenance!
PPA agreements often include maintenance of the PV system. Since the developer wants to maximize their investment, they do not want the PV panels covered in snow. They may come out and clean the roof, but foot traffic and access can damage the roof system. The owner/facility manager needs to make sure that maintenance crews are not dropping equipment or damaging the roof in the process. Additional follow-up during the maintenance of the PV system with a roof contractor or maintenance system is important to maintain the life of the roof.
Annual maintenance visits to the warrantied system should be completed. Similar to snow removal, it is important to make sure that no damage results from maintenance traffic to the systems. If the building owner owns the panels, they may need to perform some of that maintenance themselves, whether it be snow removal or panel cleaning. Single-ply roof systems can be quite slippery, especially with ice and snow, so make certain to have the appropriate walkways or access paths as well for maintenance of both the roof and PV system.
About the authors: Brian Neely, AIA, CDT, BECxP is vice president/senior associate and Jeffrey Ziske, P.E., CDT, is a project engineer with Gale Associates, Inc., a 100-person consulting firm of building enclosure experts, engineers, and architects specializing in the repair, renovation and adaptive reuse of existing buildings, sites and infrastructures. The company’s is headquartered in Rockland, Massachusetts. For more information, visit galeassociates.org.
Be the first to comment on "PVs and Their Impact on Roofing Assemblies"