The newest research facility at State University of New York at Albany is the state-of-the-art Emerging Technology and Entrepreneurship Complex (ETEC). The building was designed to bring together scientists and business leaders to find solutions for society’s most pressing challenges, including climate science, emergency preparedness and cybersecurity.
ETEC fosters collaboration among students, faculty and entrepreneurs to help build a more resilient and economically vibrant New York, and the building was designed to reflect its larger goals. At 246,000 square feet, ETEC is one of the university’s largest and most energy-efficient buildings. Durability and sustainability were key considerations for the building’s exterior facade, which features aluminum composite material (ACM) panels.
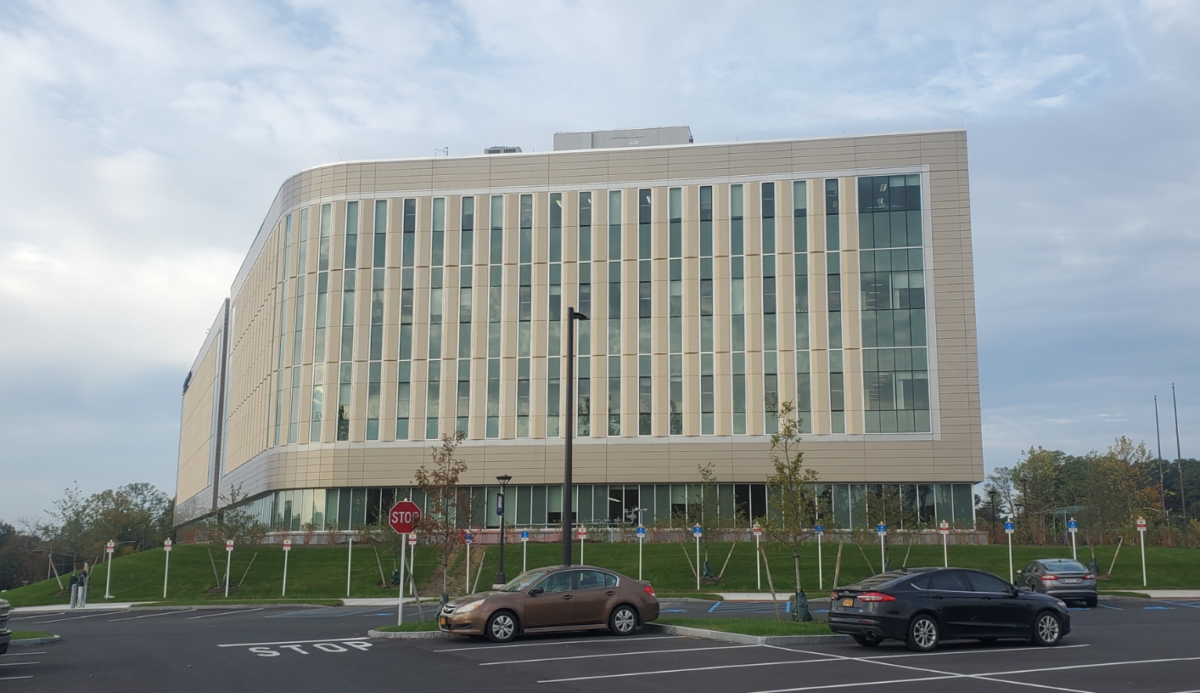
The research facility was envisioned by Cannon Design and built under the direction of Consigli Construction, which served as the general contractor on the project. For the ACM wall panel fabrication and installation, the firm tapped Charles F. Evans Company, Inc., a union-affiliated roofing contractor headquartered in Elmira, New York.
Crews from Charles F. Evans Company, Inc., fabricated and installed approximately 56,000 square feet of Alpolic ACM panels. They also applied 425 30-inch-wide GFRC Panels, which were manufactured by Plasterform. An additional 14,000 square feet of Concept Series CS-620 Centria panels were installed on the penthouse and a stand-alone maintenance building.
Booming Segment of the Market
Wall panels have been making up an increasing percentage of the company’s workload, and Charles F. Evans Company, Inc., was thrilled to be a part of this project. “We were looking for ACM projects in the area, and this one was close to us — a large-scale project that we jumped into headfirst,” President Bill Burge recalls. “It was the first time we had worked with Consigli. They are based out of Boston, and they have a satellite office in Albany, so it was a good project for them and a good project for us to start with them on. They were a real good company to work for.”
The exterior wall panel system consisted of sub-framing, mineral wool insulation, and the ACM, GFRC and Centria panels. “The sub-framing system was from Knight Wall,” Burge explains. “In between the sub-framing we used Rockwool Cavityrock, which is a mineral wool insulation. Overtop of everything we either installed the 4 mm ACM panels, GFRC panels or the Centria panels.”
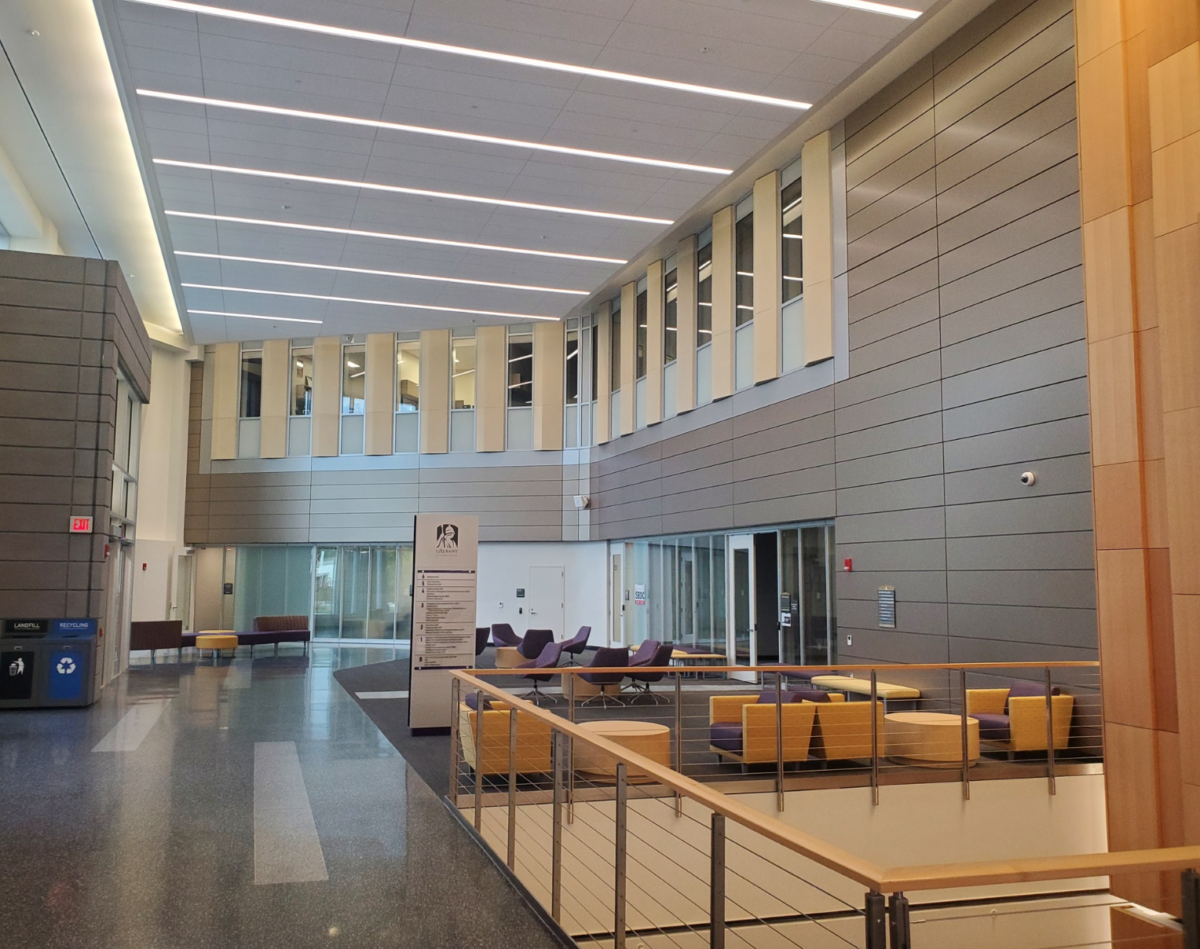
The scope of work also included some ACM and GFRC panels that were installed on the interior. “There were some small panels in the vestibule area that we put in as well,” Burge says. “The thought was to carry that design element into the interior — and bring the outside in.”
Burge cites the durability, fire rating and aesthetics of the ACM panels as their key attributes, noting that they also provide added benefits for scheduling.
“Especially in new construction, we are seeing this a lot more,” he says. “These wall panel systems allow trades to start their interior work sooner. As soon as the exterior sheathing and vapor barrier is installed, we can do all of our exterior finishes at the same time they are doing the interior finishes. Installing a sub framing system and continuous insulation on the exterior eliminates thermal bridging and creates a fire resistant, non-combustible wall system. So, from a scheduling standpoint, it allows for faster-paced production and a more energy efficient building. It’s the future — definitely.”
Installing the Panels
The wall panel installation began on the west side of the building and continued counterclockwise around the building. “We had a crew putting on the Knight Wall framing, and we had a second crew coming behind them to put the mineral wool insulation into the cavities,” Burge says. “Then we had the crew that put the framing on drop back and start installing the finished panels. The project not only kept our crews busy at the site in Albany but kept six guys busy here in Elmira, New York, fabricating the panels.”
Panels were fabricated to exact field measurements and delivered each week as the project progressed. The planks for the panels were provided by Alpolic and fabricated using a Carter Fusion extrusion system.
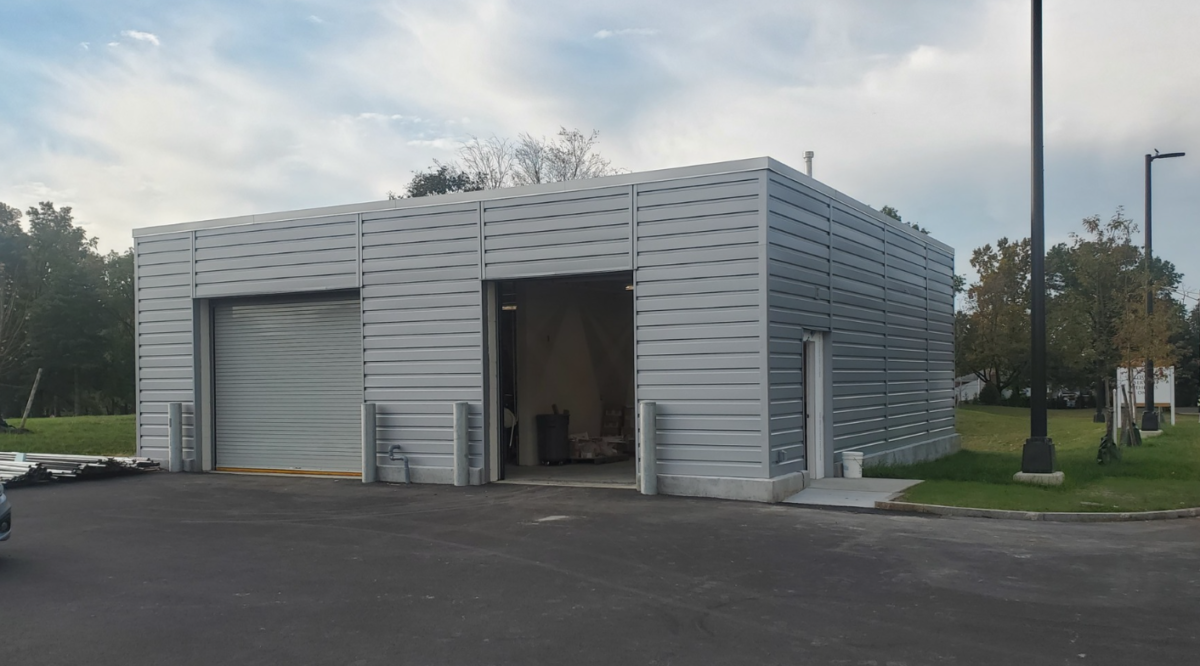
“The Carter Fusion extrusion system actually fastens right to the Knight Wall framing,” Burge says. “It’s almost like Lego blocks; you put them right on top of each other and just keep working up the wall, from bottom to top, left to right.”
The vast majority of the panels were installed from boom lifts. “Approximately 90 percent of the areas were done out of 86- or 120-foot boom lifts, depending on the access,” he notes. “On the Penthouse, we had to erect scaffolding, and for two areas over some large skylights we had to use a swing-stage scaffold.”
Safety was the top priority on the project, and crew members were tied off 100 percent of the time in boom lifts and the swing-stage scaffold.
The complex job went smoothly, according to Burge. “On a new construction project, you’re always going to have your challenges,” he says. “You’re coordinating with a lot of different trades, but overall it all went well. Your typical upstate New York weather is challenging, and this project didn’t stop over the winter. We had some very harsh conditions, and the Covid-19 pandemic posed some issues as well.”
Burge credits the project’s success to smooth coordination with the general contractor and the quality craftsmanship of Charles F. Evans Company, Inc.’s highly trained personnel. “Matt Denson was our foreman on the project, and he did a wonderful job, overseeing 12-14 guys throughout the project,” Burge says. “He did a great job for us.”
Burge believes that complex installations like this one bring out the best in the company’s crews. “We have some of the best sheet metal workers in the area,” he says. “We like unique projects, challenging projects, and we rise to the occasion when those opportunities come along. It’s something we look forward to, and our guys excel at these types of projects. The outcome speaks for itself.”
TEAM
Architect: Cannon Design, Buffalo, New York, cannondesign.com
General Contractor: Consigli Construction, Albany, New York, consigli.com
Wall Panel Installer: Charles F. Evans Company, Inc., Elmira, New York, evansroofingcompany.com
MATERIALS
Wall Panels: ACM Panel, Alpolic Materials, alpolic-americas.com
Wall Panels: GFRC panels, Plasterform, plasterform.com
Wall Panels: Concept Series CS-620, Centria, centria.com
Insulation: Cavityrock, Rockwool, rockwool.com
Sub-Framing: Knight MFI, Knight Wall Systems, knightwallsystems.com
Be the first to comment on "Wall Panels Brighten Building Envelope of New Research Facility"